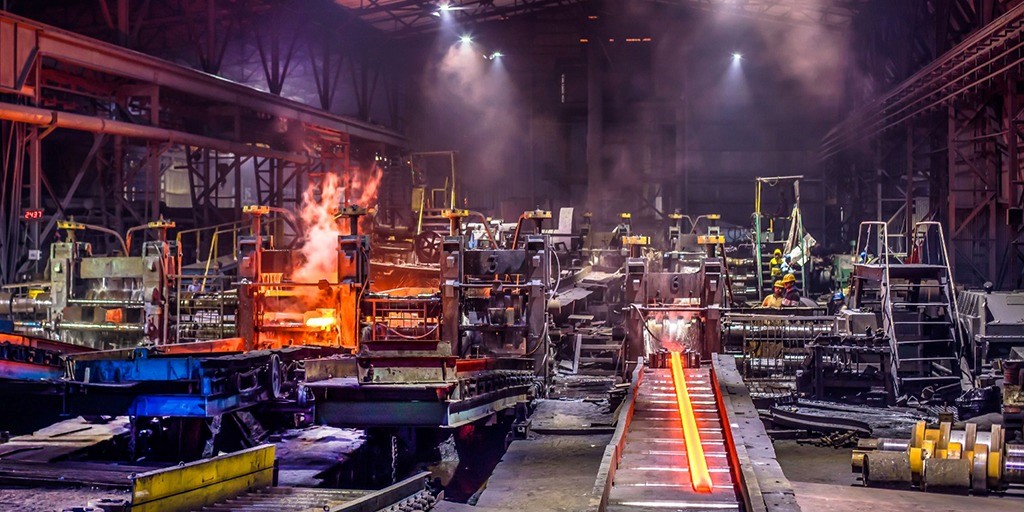
From Ore to Alloy – The Journey of Metal Production at Shyam Metalics
Nature and Variants of Metal
To understand the practicality and adaptability of metals, we need to dive deep into their technical, physical, chemical, and mechanical traits. Metals have mechanical strength for utility and chemical characteristics for environmental adaptation.
Some metals, like aluminum and stainless steel, have different properties. Aluminum is used in aerospace and electrical applications due to its lightweight and electrical conductivity. Whereas steel is a strong, recyclable iron-carbon alloy, The alloy steel increases firmness and wear resistance. Chromium-enriched stainless steel resists rust and finds application in various fields. Iron is used in construction, transportation, and other sectors for its ductility and abundance.
Production of Metal
Metal manufacturing is one of the most versatile production processes and every time something new is produced by practicing manipulation of different metals. From supplying the metal framework and beams for infrastructure to household items, most of them would not exist without metal production.
Now let us look at the process of metal production in detail.
- • Preparation
Metal production begins with iron ore, coal, and lime extraction. Hematite and magnetite ore are the main sources of iron for steel manufacturing. First, raw materials are melted in a blast furnace to make molten iron. Many impurities make this hot metal fragile and must be eliminated.
- • Forging
During forging, workers heat the hot metal to a high temperature and press it into a desired shape. Sometimes full-hand forging involves heating the metal to a high temperature. When hot, the metal takes on curves, shapes, and forms by using a hammer or punch to strike the hot metal.
- • Heat treatment
The process of heat treating metal involves changing the material properties of the metal by heating and cooling it in a specific manner. There are four main types of this process- annealing, hardening, quenching, and stress relieving.
- • Casting
Casting is the pouring of molten metal into a mould so that it can cool and retain the shape of the mould. Grid casting is the most popular process which gives the possibility of using reusable moulds for mass production.
- • Drawing
Drawing is the process of using gravity to draw metal into a conical die, which works at both room temperature and elevated temperatures. The design process exists for various materials, such as metal, plastic, and glass. This process results in the thinner metal sheets that most metal sheets come from.
- • Extrusion
Extrusion is the process of forcing metal through the cross-section of a die. The cross-section of the extruder determines the cross-section of the entire molding. This process is the most common way to make metal cylinders.
- • Forming
Forming is the bending of metal at certain points to form the desired part with a drill, hammer, and clamp. Metals that react with air are often used in this process, transforming into a liquid state without flowing. Combinations of shapes in this metal fabrication can create complex objects, such as a well-designed soda can.
- • Machining
Machining is a process that can take many forms, such as drilling, turning, or milling. It is a subtractive manufacturing technique that refers to the process of removing material to make a desired part. This entire process category of laser processing including laser drilling and laser engraving, must also be considered here.
- • Cutting
Another form of subtractive manufacturing is metal cutting. Metal cutting can be achieved in many ways, such as using lasers, water, electric scissors, and plasma on the piece of metal being cut.
- • Drilling
Drilling is the process by which a tool removes material at a specified location to a specified depth and diameter through lasers and metal tools.
- • Punching
Punching is making holes in metal parts. With dies, specially designed tools strike the metal to form the desired holes. One popular use would be to drill holes for electronics in assemblies containing electrical components.
- • Stamping
Stamping is a process in which metal is pressed, and it is effective for placing letters, shapes, or images on metal parts. This process is often the process of choice for giving sheet metal parts the indentations needed to bend certain joints.
- • Welding
Welding is the process of joining two pieces of metal using heat and/or pressure. Dissimilar metal parts are commonly joined to form complex assemblies through welding.
These complex processes have the future of metals in their hands bringing durability, functionality, and innovation to metal products.
As we look further into the metal industry, the future comes with promise and opportunities. The metal industry in India accounts for around 13% of the GDP making us self-reliant for our infrastructural development.
Shyam Metalics is proud to be India’s leading integrated metal-producing company with a consistent track record of delivering operating profitability. We operate ‘ore to metal’ steel manufacturing plants, primarily producing Iron Pellets, Sponge Iron, etc. Our plants can promptly adjust to dynamic market situations, modify our production and product offerings to suit the ever-evolving market landscape, and maximise our operating margins.